Die Casting
Common Defects in Die Casting: Causes and How to fix them
Author: The Cam Cad Co.
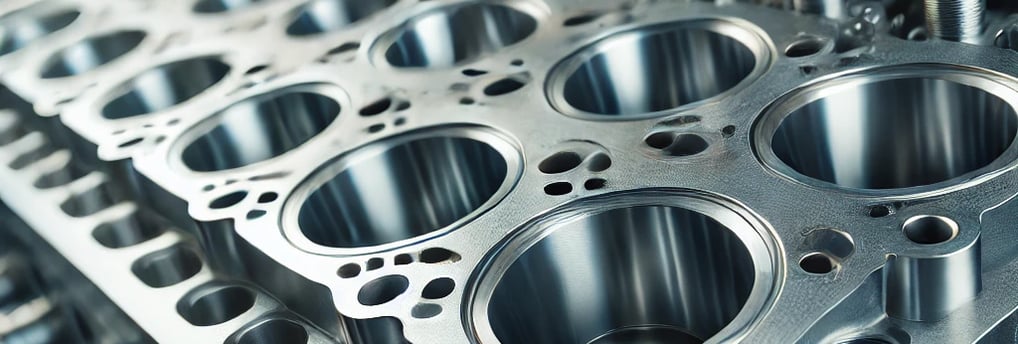
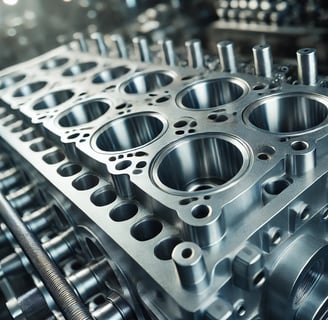
Common Defects in Die Casting: Causes and Solutions
Die casting is a highly efficient manufacturing process used to produce metal parts with precision and durability. However, like any manufacturing method, it comes with its own set of challenges. Mistakes during the process can lead to defects that affect the quality, performance, or appearance of the final product. Here’s a simple guide to common die casting mistakes, their causes, and practical solutions.
1. Porosity: Tiny Holes in the Metal
What is it?
Porosity refers to small air pockets or voids inside the cast part, which can weaken it or cause leaks.
Why does it happen?
Air is trapped during the injection process.
The metal solidifies unevenly.
Poor gating or venting design.
How to fix it:
Improve mold venting to allow trapped air to escape.
Use a vacuum die-casting process for better air removal.
Redesign the gating system to ensure smooth metal flow.
2. Cold Shut: Unbonded Layers in the Part
What is it?
Cold shut occurs when two streams of molten metal meet but don’t fuse properly, leaving a weak line or crack.
Why does it happen?
The metal is too cold when it flows into the mold.
Slow injection speed.
Poor mold design with complex flow paths.
How to fix it:
Increase the molten metal temperature.
Raise the injection speed to improve flow.
Redesign the mold to simplify flow paths.
3. Flash: Excess Metal on the Edges
What is it?
Flash is the extra metal that squeezes out along the parting line or mold edges.
Why does it happen?
Misaligned or worn-out molds.
Excessive injection pressure.
Insufficient clamping force.
How to fix it:
Align and maintain molds regularly.
Lower the injection pressure to reduce overflow.
Ensure the clamping force is strong enough.
4. Shrinkage Cavities: Internal Voids in the Part
What is it?
Shrinkage cavities are hollow spaces inside the part caused by uneven cooling and solidification.
Why does it happen?
Thick sections of the part cool slower than thin sections.
Inadequate metal feed during cooling.
Poor riser or feeder design.
How to fix it:
Design parts with uniform wall thickness.
Use chills or cooling inserts to speed up cooling in thick areas.
Improve feeder design to ensure a steady supply of molten metal.
5. Cracks: Broken or Fractured Parts
What is it?
Cracks appear in cast parts when they are subjected to high stress or improper cooling.
Why does it happen?
Uneven cooling causes thermal stress.
The mold ejects the part too early.
Poor mold design or material choice.
How to fix it:
Optimize cooling rates to reduce stress.
Wait for the part to cool fully before ejecting.
Use stronger mold materials and designs.
6. Surface Defects: Rough or Uneven Finishes
What is it?
Surface defects include rough, bumpy, or uneven finishes on the cast part.
Why does it happen?
Contaminated or low-quality molten metal.
Mold surface is damaged or improperly finished.
Metal solidifies too quickly.
How to fix it:
Use clean, high-quality materials for casting.
Maintain and polish the mold regularly.
Control the cooling rate to ensure a smooth finish.
7. Misruns: Incomplete Castings
What is it?
Misruns happen when the molten metal doesn’t fill the mold completely, leaving gaps or incomplete sections.
Why does it happen?
The metal cools and solidifies before filling the mold.
Low injection pressure or speed.
Poor gating system design.
How to fix it:
Raise the metal temperature to keep it flowing longer.
Increase injection pressure and speed.
Redesign the gating system for better flow.
8. Hot Tears: Weak, Torn Sections
What is it?
Hot tears are cracks or tears in the part caused by stress during cooling.
Why does it happen?
The mold restricts the part’s contraction during cooling.
Uneven cooling rates.
Weak mold material that can’t handle stress.
How to fix it:
Use flexible mold materials that can handle contraction.
Design molds with proper draft angles and allowances.
Optimize cooling rates to reduce thermal stress.
9. Blisters: Bubbles on the Surface
What is it?
Blisters are raised bubbles or bulges on the surface of the part caused by trapped gas or moisture.
Why does it happen?
Moisture in the mold or molten metal.
Poor venting that traps gas inside.
Excessive injection speed.
How to fix it:
Dry the mold and materials thoroughly before use.
Improve mold venting to allow gas to escape.
Lower the injection speed to avoid trapping gas.
10. Erosion: Damage to the Mold
What is it?
Erosion is the gradual wear and tear on the mold caused by high-speed molten metal flow.
Why does it happen?
Metal is injected at too high a speed.
Abrasive particles in the molten metal.
Poor mold material or coating.
How to fix it:
Lower the injection speed to reduce impact.
Filter molten metal to remove impurities.
Use high-quality, erosion-resistant mold materials.
11. Inclusions: Foreign Particles in the Part
What is it?
Inclusions are solid particles or impurities trapped in the cast part.
Why does it happen?
Contaminants in the molten metal.
Poor filtration during the process.
Improper handling of materials.
How to fix it:
Use filters to remove impurities from the molten metal.
Handle materials carefully to prevent contamination.
Maintain a clean working environment.
Conclusion
Die casting can produce precise and high-quality parts, but mistakes can lead to costly defects. By understanding these common issues, their causes, and how to fix them, manufacturers can improve product quality and efficiency. Regular mold maintenance, proper material handling, and optimized process settings are key to avoiding defects.
Have you faced any of these challenges in your die-casting projects and want expert's advice?
Feel free to contact us.
The Cam Cad Co.
Mumbai:
Raaj Chambers
New Nagardas Rd, Andheri East, Maharashtra 400069
Gurugram:
The Executive Centre
Cyber City, Tower A, DLF Phase 3, Gurugram, Haryana 122002
© 2025 TheCamCad.com. All Rights Reserved.