Injection Molding
Common Injection Molding Defects: Causes and How to Fix Them
Author: The Cam Cad Co.
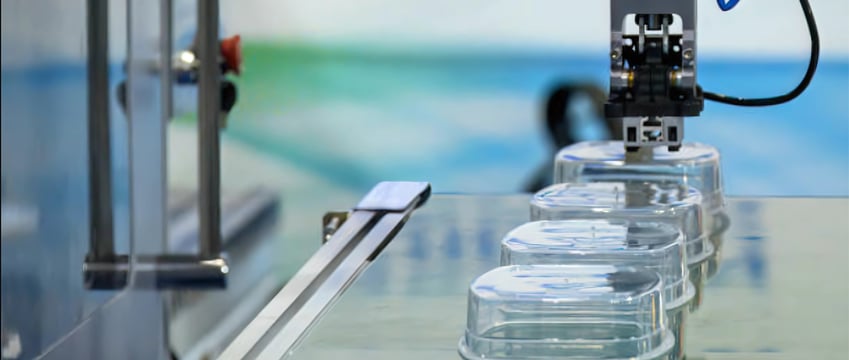
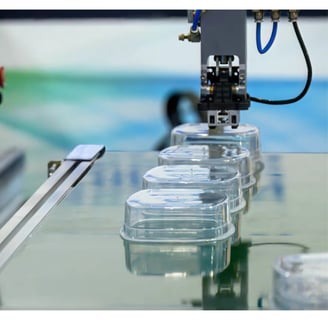
Common Injection Molding defects: Causes and How to Fix Them
Injection molding is a great way to create products efficiently, but it’s not always smooth sailing. Sometimes, defects show up in the parts, causing problems with their appearance or function. The good news? Most of these issues can be fixed if you know what’s causing them. Let’s look at common mistakes in injection molding, their causes, and simple ways to solve them.
1. Warpage: When Parts Get Twisted Or Distorted After Cooling
What is it?
Warping happens when a part bends or twists out of shape after cooling, which makes it hard to use.
Why does it happen?
Different areas of the part cool at different speeds (Uneven cooling).
The walls of the part aren’t the same thickness.
The material shrinks unevenly.
How to fix it:
Design parts with walls that are the same thickness.
Make sure the cooling system works evenly across the mold.
Use materials that shrink less and stay stable.
2. Sink Marks: Small Dents in the Surface
What is it?
Sink marks are tiny dents or dimples (depressions) that show up on the surface of thick section of the part.
Why does it happen?
The material isn’t packed tightly enough.
Cooling isn’t strong enough in thick areas.
The walls of the part are too thick.
How to fix it:
Increase the packing pressure and hold time during molding.
Use ribs or cores to make thick areas thinner.
Make sure the cooling system works well in thick sections.
3. Flash: Material Seeping Out
What is it?
Flash is extra material that leaks out of the mold and hardens where it shouldn’t.
Why does it happen?
The mold halves (core & cavity) aren’t aligned (matched) properly.
Injection pressure is too high.
The clamping force isn’t strong enough.
How to fix it:
Check the mold for alignment issues (mold matching) and fix them.
Reduce the injection pressure.
Ensure the machine applies enough clamping force.
4. Short Shots (Short Molding): When Parts Don’t Fill Completely
What is it?
Short shots (short molding) happen when the mold doesn’t fill up completely, leaving gaps in the part.
Why does it happen?
Not enough material is injected.
Narrow gates and runners.
Air is trapped inside the mold.
The material isn’t flowing well because it’s too cold (Low melt temperature).
How to fix it:
Increase the injection pressure or feed more material.
Optimize mold design by enlarging gates and runners.
Add vents to let air escape from the mold.
Raise the material temperature to make it flow better.
5. Flow Lines (Flow Marks): Visible Streaks Patterns
What is it?
Flow lines (flow marks) are streaks on the surface of the part that show how the material flowed inside the mold.
Why does it happen?
The material moves too slowly.
The mold temperature isn’t even (low mold & melt temperature).
The mold design and improper gate location forces the material to make sudden turns (Uneven flow of molten plastic).
How to fix it:
Inject the material faster.
Keep the mold temperature consistent (Increase mold and melt temperature).
Smooth out flow paths in the mold design.
6. Burn Marks: Discoloration or Dark Spots
What is it?
Burn marks are dark spots or discoloration on the part, often caused by trapped air overheating.
Why does it happen?
The mold isn’t vented well enough.
The injection speed or temperature is too high.
The cycle time is too long, causing overheating.
How to fix it:
Improve the mold’s venting system.
Lower the injection speed and material temperature.
Shorten the cycle time to avoid overheating.
7. Weld Lines: Weak or Visible Lines
What is it?
Weld lines show up where two flow fronts meet but don’t bond completely, leaving a visible line or weak spot.
Why does it happen?
The material is too cool to bond well.
The injection speed is too slow.
The mold design creates poor flow paths.
How to fix it:
Increase the material temperature and injection speed.
Adjust gate placement for better flow.
Use materials that bond more easily.
8. Delamination: Flaky Surfaces
What is it?
Delamination is when thin layers flake off the surface of the part, making it look and feel weak.
Why does it happen?
The material is contaminated or incompatible.
The material wasn’t dried properly.
Sharp changes in the mold design cause stress.
How to fix it:
Use clean, high-quality materials.
Make sure materials are completely dried before molding.
Avoid sudden changes in flow direction in the mold design.
9. Jetting: Wavy Flow Marks
What is it?
Jetting happens when the material shoots into the mold too quickly, leaving wavy marks on the surface.
Why does it happen?
The injection speed is too high.
The gate design is poor.
The mold temperature is too low.
How to fix it:
Reduce the injection speed.
Use gates that control the material flow better.
Raise the mold temperature.
10. Voids: Air Pockets Inside the Part
What is it?
Voids are air bubbles trapped inside the part, weakening its strength.
Why does it happen?
The material isn’t packed tightly enough.
The mold isn’t vented well.
Uneven cooling causes the material to shrink.
How to fix it:
Increase the packing pressure.
Add vents to release trapped air.
Make sure the cooling is even throughout the mold.
11. Bubbles: Visible Air or Moisture Pockets
What is it?
Bubbles are air or moisture trapped inside the part, creating blisters or pockets you can see.
Why does it happen?
The material contains moisture.
The mold isn’t vented enough.
The temperature is too high, causing gas buildup.
How to fix it:
Dry the materials completely before molding.
Improve venting in the mold.
Lower the temperature slightly to reduce gas formation.
12. Flash Lines on Textured Surfaces
What is it?
Flash lines are extra material that shows up on textured parts, making them look messy.
Why does it happen?
Injection pressure is too high.
The mold isn’t sealing tightly because of wear and tear.
How to fix it:
Lower the injection pressure.
Maintain and repair molds regularly to ensure a good seal.
Conclusion
Injection molding can be tricky, but most mistakes are easy to fix when you know what’s causing them. By focusing on good design, proper material handling, and regular mold maintenance, you can avoid defects and create high-quality parts every time.
If you’ve experienced these issues, and want expert's advice, feel free to contact us.
The Cam Cad Co.
Mumbai:
Raaj Chambers
New Nagardas Rd, Andheri East, Maharashtra 400069
Gurugram:
The Executive Centre
Cyber City, Tower A, DLF Phase 3, Gurugram, Haryana 122002
© 2025 TheCamCad.com. All Rights Reserved.